High-Precision and Built-In Environmental Benefits
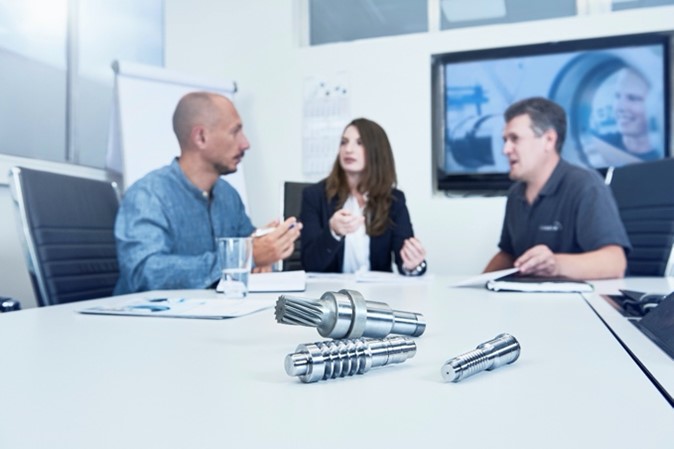
In a four-part blog series, development of
whirling machines, we will discuss profitability, technical possibilities, applications, innovation, environmental protection, and market development of whirling machines.
In the metalworking industry, whirling is no longer the coarse complementary process to grinding that it was in the past. Today it’s an efficient high-precision process that not only makes grinding unnecessary in most cases, but also offers additional advantages – especially for companies that take sustainability and efficiency seriously. Anyone who wants to make their manufacturing company fit for the future should have whirling machines in mind when it comes to new equipment acquisitions or the replacement of grinding machines.
There are rotors and
screws of all sizes that are made of various materials that can be completely manufactured with whirling. A whirling machine can produce a variety of designs. Examples include
ball screws that are used in the aerospace industry, production of linear slides of various sizes, and precision spindles for all application areas.
The addition of a whirling machine to a company’s manufacturing capabilities, provides the opportunity to cross over into other market segments that were previously out of reach. Mechatronics is advancing into more areas where spindles and screws are important components. The use cases for ever smaller components are increasing in automotive
applications, medical technology, and robotics. Precision expectations are high and will continue to increase, making Whirling Machines a perfect choice.
Precision in One Operation
Modern whirling processes produce helical geometries in just one step – without subsequent grinding or polishing. Heat generated through cutting is largely dissipated with the chips, so the workpiece does not get so hot and change the surface properties of the material – a crucial requirement with hardened parts.
The low heat cutting action means the workpiece can be processed dry, without the use of coolant or cutting lubricants. The finished piece comes out of the machine free of liquid residue and does not have to be cleaned separately. This is one example of a cost advantage and there are benefits in environmental protection and occupational safety as well.
Environmental Benefits from Whirling Process
Since no cooling lubricants are used in whirling, there is no hazardous waste. Manufacturing companies would have to handle those materials properly and have them disposed of by a specialized company. These considerations aren’t needed using the whirling process.
Raw Material vs Hazardous Waste
If threaded spindles and worms are manufactured by grinding, this process requires a large amount of coolant due to the abrasive cutting action. This process is complex and cost-intensive due to the grinding sludge that is created.
The grinding sludge is a mixture of used liquid – an oil or an emulsion – and the grinding wheel abrasion of the workpiece material in different grain sizes. Much of the liquid can be recovered by pressing processes such as briquetting. But these pressing processes require special systems and additional work steps. With the use of whirling machines, both are eliminated. The pressed grinding sludge residue are classified as hazardous waste and is often expensive to dispose of.
Whirling is completely different because the whirling chips are dry and can be recycled, untreated. The material value is retained, and the chips are not waste that the manufacturing company has to pay for, but rather a material that can be sold to a scrap dealer.
Environmental Concerns
Today companies are more aware of their environmental footprint and associated costs, using less water-polluting substances such as coolant is important because of the damage to the company image and impact on business it may cause. Companies do not want to be associated with companies that have environmental issues, this means an incident can cost orders and even customer relationships.
Reducing the amount of problematic operating material with a more modern machining process not only strengthens the relationship between the community and the company, it also makes customers feel more inclined to do business with the manufacturer.
Occupational Safety
Occupational safety is another major corporate concern. Machinery in general must adhere to very high standards to protect employees. When looking at options, operating materials used in grinding machines pose a risk that whirling machines do not. The use of water-miscible or water-mixed cooling lubricants, can result in N-nitrosamines. Skin contact with the liquids can cause allergic reactions.
When used, the cooling agents are atomized and vaporized, mixing into the air we breathe – both in the factory and in the vicinity of the company. These resulting mists can multiply into an airbourn bacterium and possibly enter the employee’s respiratory tract.
Whirling as a dry process and avoids all of these dangers and reduces the number of regulations that employees in production and logistics must comply with.
New Opportunities/Lower Costs
Dry whirling offers advantages to companies that have replaced part of their grinding machines with whirling machines. Some companies have outsourced the production of spindles and screws because of the coolant problem. With the acquisition of a whirling machine, manufacturing companies have taken back production of these components which is a clear advantage in streamlining the supply chain and operation modernizing.
Even beyond the above described production
benefits and logistical advantages Whirling provides, simply stated Whirling reduces overall manufacturing costs.