Ball Screw Whirling Replaces Thread Grinding
Leistritz has developed a unique process solution of combining precision follower rests, an economic resharpenable tool system and high-speed whirling heads with a rigid and accurate CNC controlled machine tools. With bed lengths up to 8m, long ball screws can be whirled to finish tolerances in a single pass in full material. By clamping the finished outer diameter in carbide “V” jaws, the follower rests on either side of the cut, guaranteeing near zero concentricity of the thread.
Ball Screw CNC Machines: No Coolant Needed
Whirling is a dry cutting process and coolant is not used, thus saving the expense of maintaining a coolant system and disposing of toxic grinding swarf. The tangential cutting action of the whirling process combined with optimum speeds and feeds, permit machining of steels as hard as 65 HRC with minimal heat transferred to the workpiece. After whirling, the material is only slightly warm to the touch with an increase in temperature of approximately 20-25°F above ambient. Since whirling is done by cutting from the tailstock towards the chuck, any slight lead variation due to this temperature increase is “behind” the cut and will not affect the cool stable bar yet to be whirled. Lead accuracies of ±0.0005″/foot are easily attained when cutting stable materials. Leistritz ball screw CNC machines are laser-calibrated at the factory and installation site to ensure positioning accuracy.
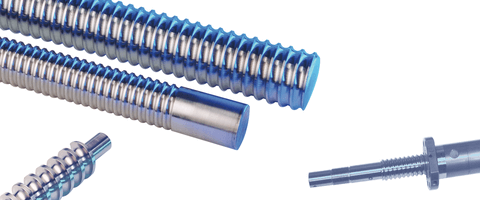
Many manufacturers using the whirling process to produce both aerospace flight control actuators and commercial ball screw assemblies for linear motion control have discovered a huge cost saving advantage. Whirling eliminated several process steps including the following:
- Part handling
- Costly grinding operations
- Roughing operations required to produce ball threads in hardened materials
Hard part whirling is a done in one operation and uses CBN cutting inserts with either a full round or gothic arch profile; this allows operators to produce finish quality screws in a single pass.
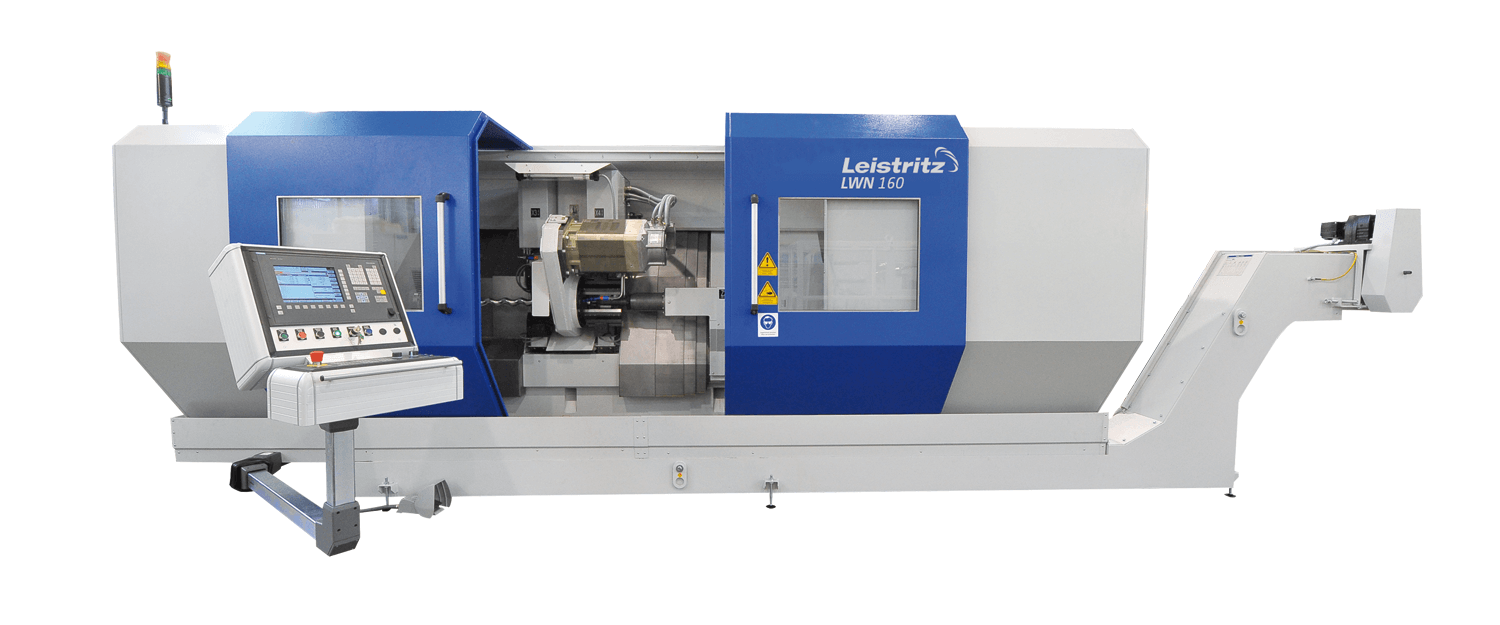
Benefits of Ball Screw Machining
Ball forms of 0.062″ ball to 0.500″ have been efficiently whirled in this manner with a huge time savings when compared to grinding. Leistritz whirling machines can offer an 8 to 10 times savings factor over thread grinding without any fear of surface cracking. Since whirling uses ideal cutting geometry, the material never reaches a critical temperature and stress does not enter the work. Screws that are whirled have excellent surface finishes down to Ra 8 microinches and are not visibly different to ground screws.