The Evolution of Whirling
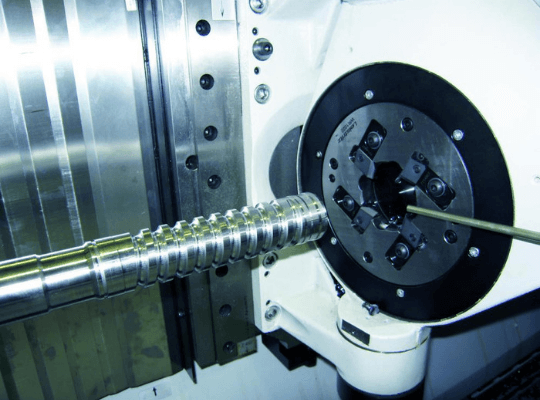
In a four-part blog series, development of
whirling machines, we will discuss profitability, technical possibilities, applications, innovation, environmental protection, and market development of whirling machines.
As the demand for higher quality machining and faster cycle times grow, so too is the need for new technology. Technology advancements has made it possible for whirling to deliver the necessary high precision rotationally symmetrical shaped parts such as EPS (Electrical Power Steering) worms and threaded spindles. These advancements include machine rigidity, control accuracy and tool design have all contributed to the increase in whirling accuracy that has all but eliminated the need to grind. At one time whirling was not the high-precision process it is today.
The better the finish, the greater the effort and cost to achieve it. Whirling delivers the necessary high precision, high surface finishes for rotationally symmetrical shaped workpieces such as EPS worms and threaded spindles. A final grinding is no longer necessary, leading to lower unit costs. But whirling was not always the high-precision process it is today.
Galileo Galilei, the great Italian physicist and engineer, devised the first machine around 400 years ago based on the principle of whirling. With it, wooden spindles for wine presses were produced in large numbers for the wine-growing regions of Italy. Industrial whirling machines for metal cutting appeared in the first half of the 20th century. As with hard milling and hard turning, large cutting forces occur with hard whirling. This requires an extremely stable machining platform and secure clamping of the workpiece and applying the right tool. The influence of the radial displacement forces when machining longer workpieces with a small diameter is eliminated by the stable clamping using centering rests.
Now fast forward to the late 20th century where whirling began being used on a much larger scale, but the surface quality achieved was not keeping up with industry requirements for better finishes. Parts still had to be reground in a second step processes. With today’s whirling machine technology, the second step is no longer necessary because of advancements in machine tool design engineering and the refinement of hard cutting process. This has taken whirling to the “one and done” process that many customers are seeking. No longer is whirling a roughing or partial process in hardened and exotic materials.
Whirling is a special form of milling. During whirling, both the tool and the workpiece rotate. With external whirling, the whirling ring rotates at high speed around the slowly rotating workpiece. At the point of contact, the axes of the vortex ring and workpiece are both offset and inclined. The swivel angle of the whirling unit determines the pitch of the resulting spindle or worm.
The axis offset determines the cutting depth. Whether right-hand or left-hand thread depends on how the workpiece rotates and whether the vortex ring is cut from above or below.
On the whirling head, which is designed as a ring for external whirling, the cutting edges sit symmetrically opposite one another and, for external whirling, point inwards towards the workpiece. Depending on the processing, cutting edges for all three processing steps – pre-cutting, final cutting and profile transition – are mounted in the ring. Typically, seated opposite each other in pairs.
When whirling a thread profile inside a diameter, the cutting tool on the whirling head points outwards. The processing principle is the same. The desired threads can be cut into cavities such as bores or pipes, for example a multi-start internal thread for ball screw nuts.
The Advantages of Whirling
As with milling, whirling produces short comma shaped chips. This is particularly advantageous when manufacturing internal geometries: the chips can be removed easily, and the risk of chip accumulation is low. In addition, the entry and exit chip strengths approach zero, which means that only low cutting forces act on the workpiece providing a reduction in elastic deformation.
The majority of the machining heat flows away from the part and into the chips. Incidentally, 100 percent of the chips can be returned to the recycling cycle. While the workpiece only heats up slightly, glowing chips with a temperature of sometimes over 1000° F may be reached. For the workpiece, this means that its surface properties remain practically unchanged. This makes the process ideal for processing hardened materials.
Most hard materials are machined without cooling lubricants due to CBN inserts being thermal shock sensitive. With grinding burns or tension marks on the part surface are common due to the processing pressure, these marks do not occur when whirling. It is these advantages that not only give the vortex process the ability to expand, they were also the driving force behind developing the high-precision process it is today.
From Preprocessing to Finishing
For a long time, whirling was the method of choice when it came to removing large quantities of material quickly, especially with large workpieces such as extruder screws and press spindles. However, this had to be followed by the final grinding step.
Two different machining processes for the production of a workpiece require not only the time-consuming procedure of re-clamping, but also the acquisition and operation of two different machines. In the past, anyone who wanted to avoid this double effort was forced to opt out of whirling and in favor of only grinding, because the ultimately necessary surface quality could only be achieved with grinding. In return, the extremely long grinding processing time coupled with higher operating costs and additional resources needed for waste disposal, were accepted as a part of just doing business.
With the Leistritz high-precision whirling equipment, just the opposite is true — whirl instead of grind. Viewed as a new type of machining process, a DIN class 6 gear is achieved by having a number of profile specific inserts evenly spaced and mounted into the cutting ring producing a high-quality surface finish all in one simple setup. There is no need to remove, relocate to a different machine and re-clamp the workpiece. Because of this, cycle times are drastically reduced when compared to grinding.
The amount of thread profiles and geometries that can be technically generated is limitless. The fourth and last article in this series deals with the workpiece diameters, swivel angles, profile goods, and more that can be achieved.
In the past we had grinding, today we have whirling. Leistritz is the global leader when it comes to setting the standard in whirling machine technology.
Problems Solved with Whirling
The whirling process primarily solves classic, technical and economic dilemmas of grinding by reducing heat and eliminating cooling lubricants.
Grinding consumes a lot of energy, which heats the workpiece and the cutting material. The higher the requirements for accuracy, the finer the grinding must be, and the more cutting heat is generated. Coolant and lubricants are used so that the heat does not adversely affect the material properties, increases the set-up times, the operating costs and disposal costs as well as the logistical cost increase.
Please check out the other blogs in this series:
Blog #1: High-Precision and Built-In Environmental Benefits
Blog #2: Savings Through Technology