Mud Motor Rotor
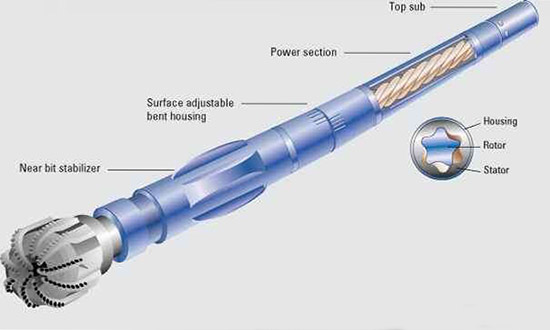
Improving Rotor Performance
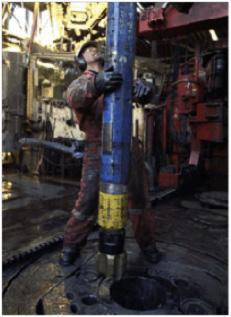
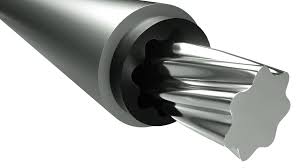
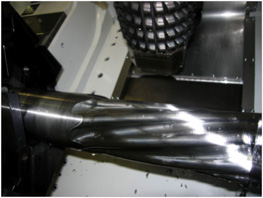
Additionally, Leistritz machines also have a milling function as a secondary alternative within the machine tool function. The flexibility of milling allows manufacturers to maintain their known process and add hob tooling as desired for their more commonly produced sizes.
The improved rigidity of the Leistritz machine provides for increased cutting speeds & feeds, reducing the milling cycle times by 30-40%.
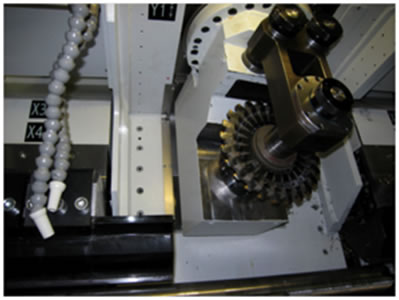