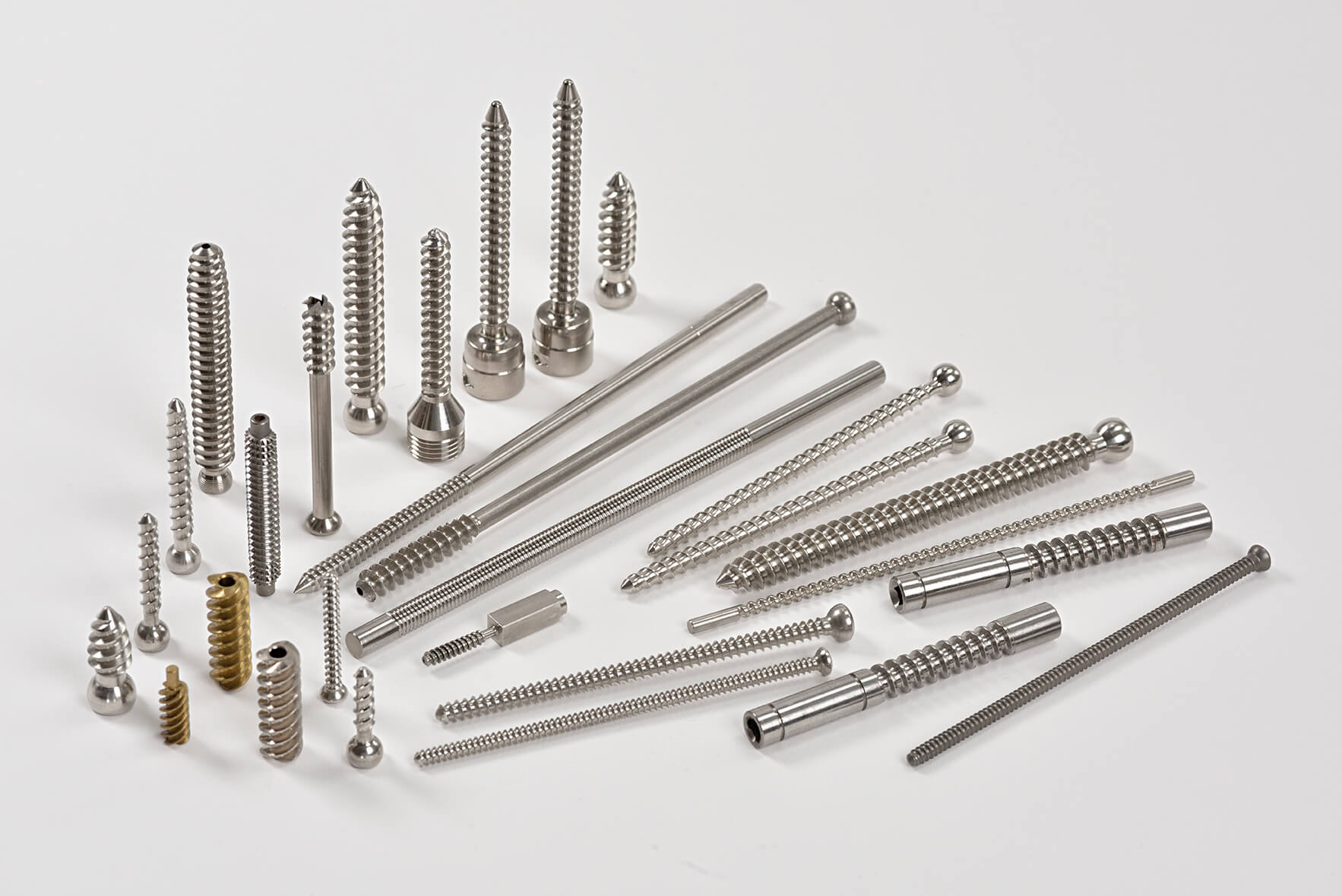
Whirling is a machining operation where a series of profiled cutters remove material by passing over the moving workpiece and advancing to produce a helical form. Whirling removes material similarly to milling; however, the carbide cutters are arranged along the inside of a ring to a predetermined cutting-circle diameter. The whirling head is tilted to the nominal helix angle.
Material removal results when the whirling ring rotates at high speed around the slowly rotating workpiece. Combined with the advancement of the longitudinal slide, this process produces the required pitch of the worm. The eccentric amount of the centerline to the whirling ring determines the pitch diameter.
Whirling Provides A Faster, More Efficient Method to Produce Bone Screws
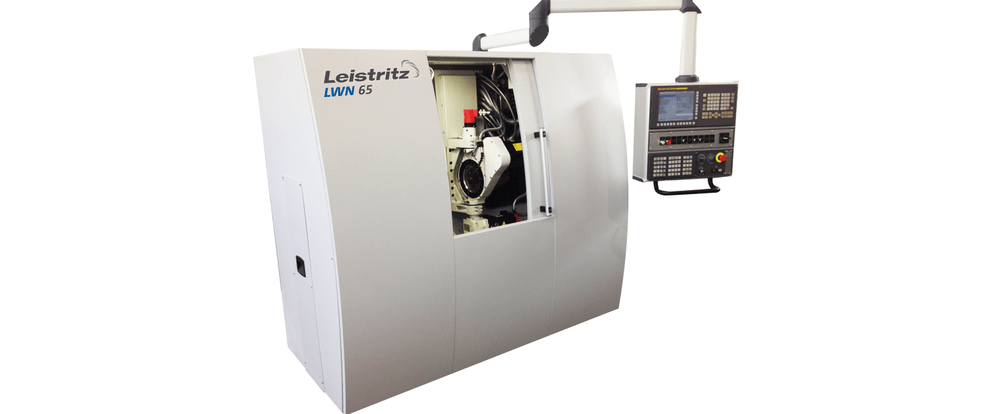
The tangential cutting action of the whirling process leaves the tool in contact with the workpiece for a much longer time along the arc of the insert’s cutting circle. Subsequently, each pass of the insert removes 4x to 6x the amount of material. Additionally, the tangential cutting action permits much higher cutting speeds, again shortening cycle times. The low approach angle of the insert, when it first makes contact with the material, contributes to the whirling tools’ longer life.
Characteristics of this process combine to give users another benefit: dry machining. In most cases, the whirling process is done dry. Without the use of coolants or cutting oils, the blue-colored, comma-shaped chips carry away nearly all of the heat generated by the cutting action.
Many shops don’t approach bone screw production with a dedicated whirling process, and this may be a mistake. Instead, shops combine manufacturing operations, but they suggest that in many situations, separating operations is a faster, more economical method for producing bone screws.
Combining manufacturing operations such as milling, turning, and whirling only makes sense if there is no cycle time compromise. The very features that make Swiss-type turning centers unbeatable for turning small diameter and long screws are exactly what make them less efficient whirling machines.
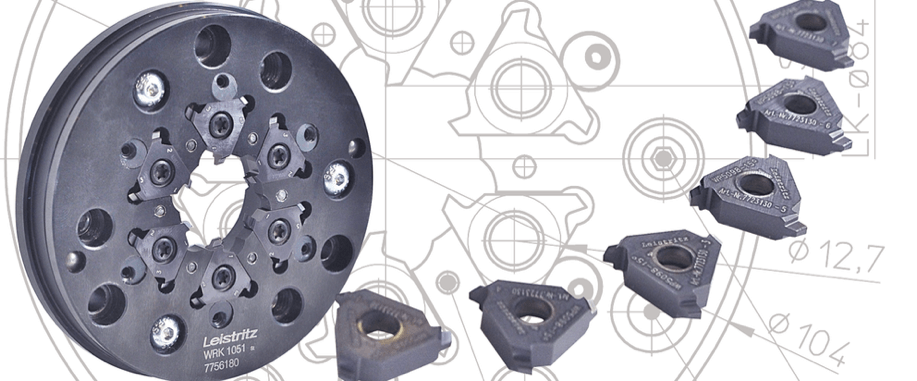
Feeding the bar material through a guide collet has the disadvantage of not permitting continuous rough- and finish-turning across a long length. Therefore, whirling a long screw requires incremental turning and whirling steps until the whole screw length is achieved, or it requires whirling the screw without first turning the blank to the thread major diameter first. Both alternatives are not only time consuming but also inaccurate, leaving a poor-quality bone screw with less than ideal surface finish.
Instead, Leistritz offers up dedicated whirling. The correct method is to turn bone screw blanks in Swiss type turning centers without the thread. These blanks would be completed screws except for the thread. Removing the threading from the turning operation provides a much shorter cycle time and greater throughput of each machine.
Next, operators can machine the thread with a dedicated whirling machine. Leistritz machines have the necessary supports to permit whirling of screws with any profile in virtually unlimited lengths in the shortest possible time.
Whirling with the correct machine can outperform whirling in a turning center by a factor of 3:1 and possibly even 4:1. Most bone screws – even in their longest designs and in either 316L stainless steel or titanium – are whirled in less than 40 seconds. What’s important to know is that the same screw would require 150 seconds to whirl in a non-dedicated whirling machine.
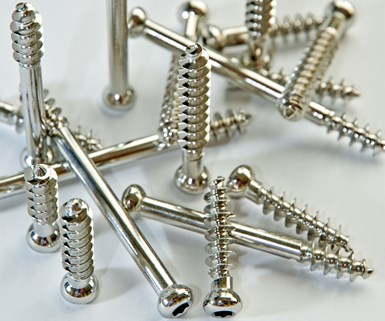
The Leistritz LWN-65-MED machine offers an automatic parts loader and hopper system. The pre-turned blanks are randomly placed into a hopper, which aligns and guides them tip-first to the staging area. Once on deck for the loading process, each screw is measured for length with a light beam and the proper CNC program is selected to run the appropriate screw length. This is a valuable tool since nearly all bone screws are produced in families of the same diameter, but in various lengths. Typical bone screws of the same family vary only in length, from 10mm to a maximum of 120mm in 5mm increments. With the Leistritz LWN-65-MED machine, all screws within the same family can be produced randomly without any setup between.
This processing also allows cell integration of a number of turning centers to each whirling machine. Typically, three or possibly four turning centers produce the blanks (of various lengths) for a single LWN-65-MED whirling machine.
Many high-volume medical screw manufacturers use the Leistritz methodology to produce bone screws in a more productive manner. When production volumes increase to the point where more than one turning center is required, this separation of operations saves the most by maximizing the utilization of all machines in a cell. The low tooling costs combined with short cycle times and no setup time really proves beneficial.